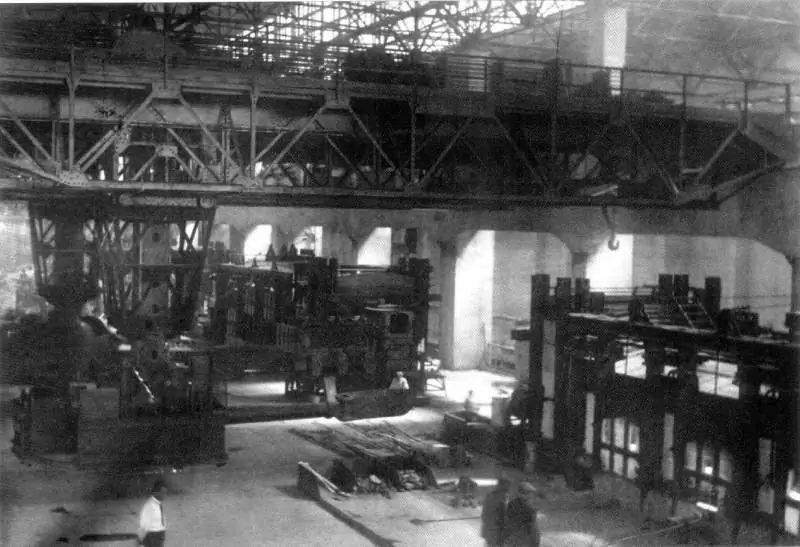
Strateški resurs
Teško je precijeniti proizvodnju visokokvalitetnog čelika za vojno-industrijski kompleks u ratnim uvjetima. Ovo je jedan od najvažnijih čimbenika uspjeha vojski na bojnom polju.
Kao što znate, Kruppovi metalurzi bili su među prvima koji su naučili proizvoditi visokokvalitetni čelik oružja.
Nijemci su usvojili proizvodni proces Thomasa krajem 19. stoljeća. Ova metoda taljenja čelika omogućila je uklanjanje nečistoća fosfora iz rude, što je automatski povećalo kvalitetu proizvoda. Kvalitetni oklop i čelik oružja tijekom Prvog svjetskog rata često su osiguravali superiornost Nijemaca na bojnom polju.
Za organizaciju takve proizvodnje bili su potrebni novi vatrostalni materijali koji su obložili unutarnje površine peći. Nijemci su koristili najnovije vatrostalne materijale magnezita za svoje vrijeme, podnoseći temperature veće od 2000 stupnjeva. Takve tvari veće vatrostalnosti temelje se na magnezijevim oksidima s malim dodacima oksida aluminija.
Početkom 20. stoljeća zemlje s tehnologijama za masovnu proizvodnju vatrostalnih materijala od magnezita mogle su si priuštiti proizvodnju visokokvalitetnih oklopa i cijevi topova. To se može usporediti sa strateškom prednošću.
Niže u smislu vatrootpornosti bili su takozvani visoko vatrostalni materijali koji podnose temperature od 1750 do 1950 stupnjeva. Riječ je o vatrostalnim materijalima od dolomita i visokog glinice. Šamotni, polukiselinski, kvarcni i dinas vatrostalni materijali mogu izdržati temperature od 1610 do 1750 stupnjeva.
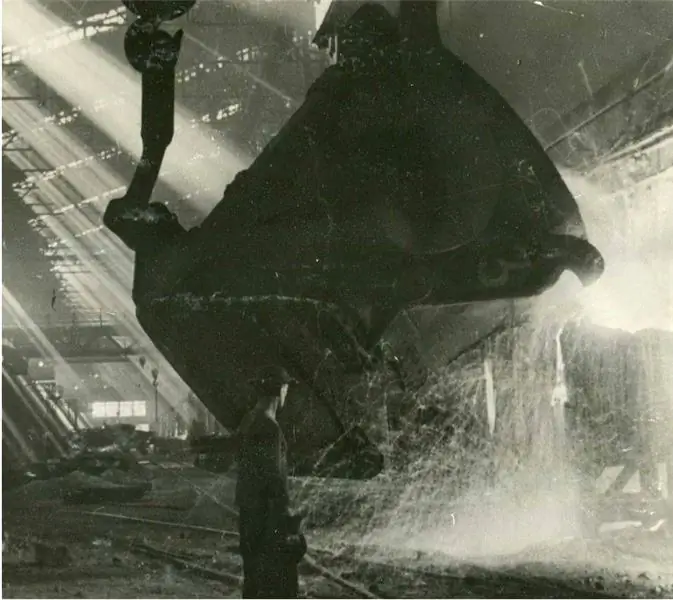
Usput, tehnologije i mjesta za proizvodnju vatrostalnih materijala od magnezita prvi su se put pojavili u Rusiji davne 1900. godine.
Satka magnezit vatrostalna opeka 1905. godine nagrađena je zlatnom medaljom na Svjetskoj industrijskoj izložbi u Liegeu. Proizveden je u blizini Čeljabinska u gradu Satka, gdje se nalazilo jedinstveno nalazište magnezita.
Mineral periklaze, od kojeg su vatrostalni materijali izrađeni u tvornici, bio je visoke kvalitete i nije zahtijevao dodatno obogaćivanje. Kao rezultat toga, vatrostalni materijal od magnezita iz Satke bio je superiorniji od svojih kolega iz Grčke i Austrije.
Premošćivanje jaza
Unatoč prilično visokoj kvaliteti magnezitne opeke iz Satke, sve do 30-ih godina glavni vatrostalni materijali sovjetskih metalurga bili su dinas materijali od gline. Naravno, postizanje visoke temperature za taljenje čelika oružja nije uspjelo-obloga unutrašnjosti peći na otvorenom tlu se raspala i zahtijevali su izvanredne popravke.
Nije bilo dovoljno cigle Satka, a u postrevolucionarnom razdoblju glavne proizvodne tehnologije su izgubljene.
U isto vrijeme, Europljani su krenuli naprijed - na primjer, austrijski Radex magnezit odlikovao se izvrsnom vatrootpornošću.
Sovjetski Savez je kupio ovaj materijal. Ali bilo je nemoguće dobiti analog bez tajne proizvodnje. Ovim se problemom pozabavio diplomant Moskovskog državnog tehničkog sveučilišta. N. E. Bauman Aleksej Petrovič Panarin. U tvornici Magnet (bivši Satka Combine) 1933. vodio je Središnji biljni laboratorij. A pet godina kasnije pokrenuo je masovnu proizvodnju vatrostalnih materijala s periklaz-kromitom ili kromomagnezitom za otvorene peći.
U Metalurškom pogonu Zlatoust i Moskovskom čekiću i srpu, Panarinov vatrostalni materijal zamijenio je zastarjele dinastije.
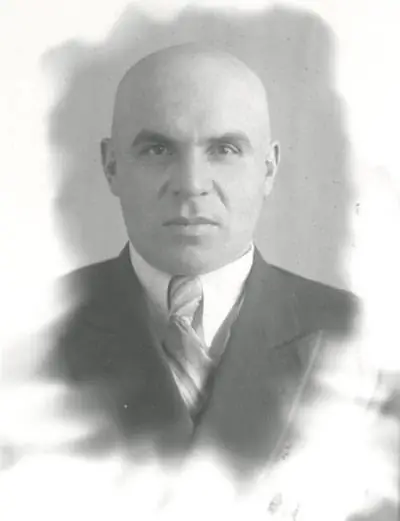
Tehnologija, koja se nekoliko godina razvijala u laboratoriju "Magnezita", sastojala se u posebnom sastavu i veličini čestica.
Prije je tvornica proizvodila konvencionalne krom-magnezitne opeke, koje se sastoje od magnezita i krom-željezne rude, u omjeru 50/50. Tajna koju je otkrila Panarinova grupa bila je sljedeća:
„Ako se kromitna ruda u grubim granulometrijskim zrnima s minimalnim udjelom frakcija manjim od 0,5 mm doda običnom naboju magnezita, tada se čak i s 10% dodatkom takve rude toplinska stabilnost opeke naglo povećava.
S povećanjem dodavanja kromitne rude grube granulometrije, stabilnost cigle raste i doseže maksimum pri određenom omjeru komponenti."
Kromit za novi vatrostalni materijal vađen je u rudniku Saranovskoye, a periklaza se nastavila vaditi u Satki.
Za usporedbu, obična "predrevolucionarna" cigla od magnezita izdržala je temperature 5-6 puta manje od Panarinove novosti.
U kirovogradskoj tvornici za topljenje bakra vatrostalni krom-magnezit u krovu odjeknuće peći izdržao je temperature do 1550 stupnjeva 151 dan. Ranije su se vatrostalni elementi u takvim pećima morali mijenjati svakih 20-30 dana.
Do 1941. savladana je proizvodnja velikih vatrostalnih materijala, što je omogućilo upotrebu materijala u velikim pećima za izradu čelika na temperaturama do 1800 stupnjeva. Važan doprinos tome dao je tehnički direktor "Magnezita" Alexander Frenkel, koji je razvio novu metodu pričvršćivanja vatrostalnog materijala na krovove peći.
Vatrostalni materijal za pobjedu
Krajem 1941. metalurzi iz Magnitke ostvarili su dosad nezamislivo-prvi put u povijesti svladali su taljenje oklopnog čelika za tenkove T-34 u glavnim teškim pećima na otvorenom.
Glavni dobavljač vatrostalnih materijala za tako važan proces bila je Satka "Magnezit". Nepotrebno je govoriti o ratnim poteškoćama, kada je trećina tvorničkih radnika pozvana na front, a država je zahtijevala da se plan prekomjerno ispuni. Ipak, tvornica je radila svoj posao, a Panarin je 1943
"Za ovladavanje proizvodnjom visoko vatrostalnih proizvoda od lokalnih sirovina za željeznu metalurgiju"
godine dobio Staljinovu nagradu.
Godine 1944. ovaj će metalurg-istraživač razviti tehnologiju za proizvodnju visokokvalitetnog magnezitnog praha "Extra". Ovaj poluproizvod korišten je za pripremu prešanog vatrostalnog materijala koji se koristi u posebno važnoj proizvodnji oklopnog čelika u električnim pećima. Granica temperature za takve vatrostalne materijale dosegla je 2000 stupnjeva.
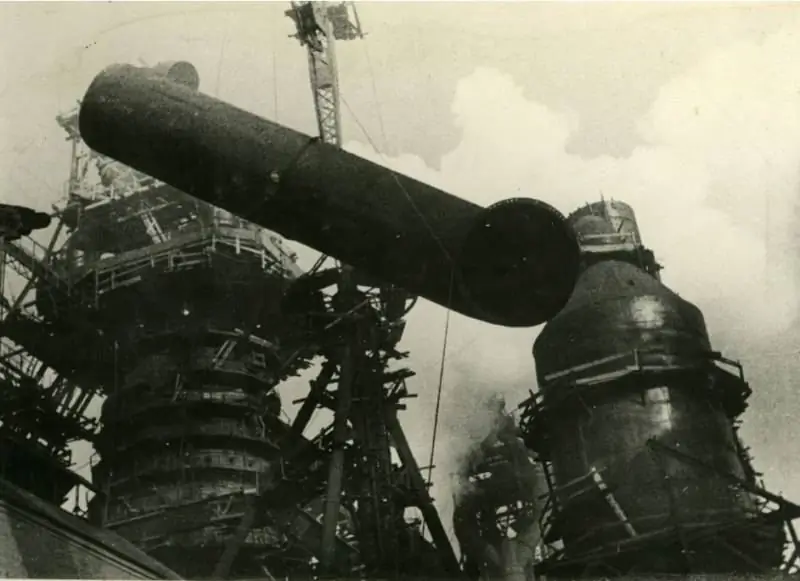
No ne treba pretpostaviti da se primjer općenito uspješne tvornice Magnezit proširio na cijelu vatrostalnu industriju Sovjetskog Saveza.
Posebno teška situacija razvila se na Uralu, gdje je praktički cijela zgrada tenkova u zemlji evakuirana 1941-1942.
Metalurški pogoni Magnitogorsk i Novotagilsk preusmjereni su na proizvodnju oklopa, opskrbljujući proizvode Sverdlovsk Uralmash, čeljabinski "Tankograd" i tvornicu tenkova u Nižnjem Tagilu broj 183. Istodobno, metalurški pogoni imali su vlastitu proizvodnju vatrostalnih materijala od lokalnih sirovina..
Na primjer, u Magnitki je tvornica dinas-chamotte proizvodila 65-70 tisuća tona opeke godišnje. To nije bilo dovoljno čak ni za njihove vlastite potrebe, a da ne spominjemo zalihe drugim poduzećima.
Prve poteškoće nastale su kada su tvornice spremnika počele graditi vlastite peći za grijanje i toplinsku energiju. Uralska metalurgija je jedva imala dovoljno vatrostalnih materijala, a zatim je za proizvodnju trupa tvornica spremnika bio potreban visokokvalitetni materijal za oblaganje peći.
Ovdje nije bilo govora o bilo kakvim vatrostalnim materijalima od kromomagnezita - ovog materijala je nedostajalo, pa čak i izvozi u zamjenu za američki Lend -Lease. Bar se to spominje u brojnim izvorima. Uralski povjesničari pišu da bi Panarinov skupi kromomagnezit mogao otići u inozemstvo u zamjenu za oskudne ferolegure za oklop tenkova. No, za to još nema izravnih dokaza.
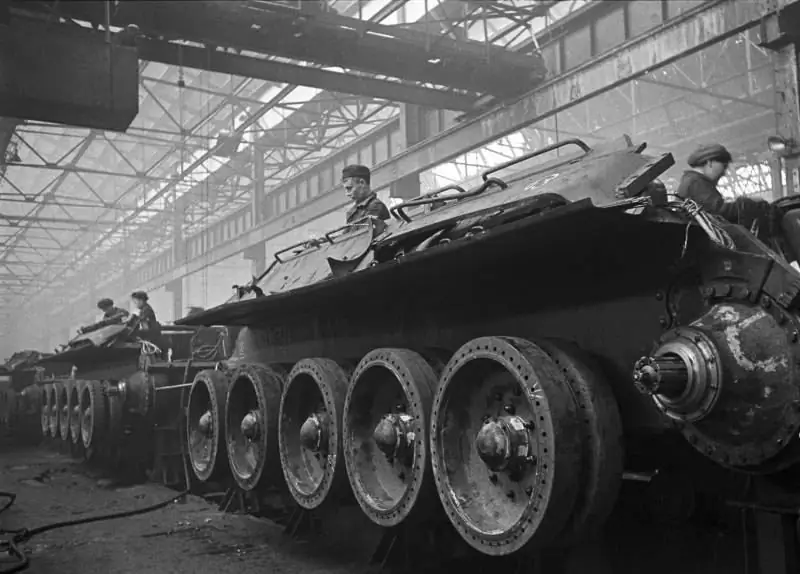
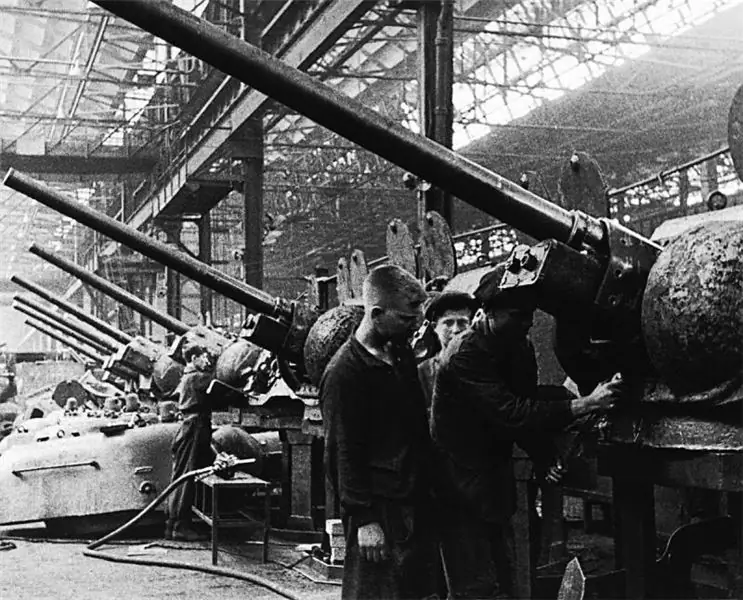
Tvornice spremnika uglavnom su se oslanjale na dinaste vatrostalne materijale proizvedene u tvornici Pervouralsk. Ali, prvo, proizvodilo se samo 12 tisuća tona mjesečno, a drugo, metalurzi su preuzeli lavovski dio.
Širenje proizvodnje u tvornici Pervouralsk išlo je vrlo sporo. A do sredine 1942. pojavile su se samo 4 nove peći. Ostali ili nisu bili spremni ili su općenito postojali samo u projektima.
Vatrostalni materijal za otvorene peći tvornica spremnika često je dolazio loše kvalitete, ne u potpunosti i u krivo vrijeme. Samo za popravak peći Uralmash u četvrtom tromjesečju 1942. bilo je potrebno 1035 tona vatrootporne opeke, a primljeno je samo oko 827 tona.
Godine 1943. trgovina na otvorenom u Uralmashu općenito je gotovo prestala zbog nedostatka vatrostalnih materijala za popravak.
Kvaliteta vatrostalnih materijala isporučenih tijekom rata ostavila je mnogo za želju. Ako je pod normalnim uvjetima dinas opeka na otvorenoj peći mogla izdržati 400 grijanja, tada u ratnim uvjetima nije prelazila 135 grijanja. A do ožujka 1943. taj je parametar pao na 30-40 zagrijavanja.
Ova situacija jasno pokazuje kako nedostatak jednog resursa (u ovom slučaju vatrostalnog) može ozbiljno usporiti rad cijele obrambene industrije. Kao što kandidat povijesnih znanosti Nikita Melnikov piše u svojim djelima, u ožujku 1943. tri su otvorene peći Uralmasha još uvijek stale i izvršile cijeli ciklus popravnih radova. Bilo je potrebno 2346 tona dinara, 580 tona šamota i 86 tona nedostatnog magnezita.
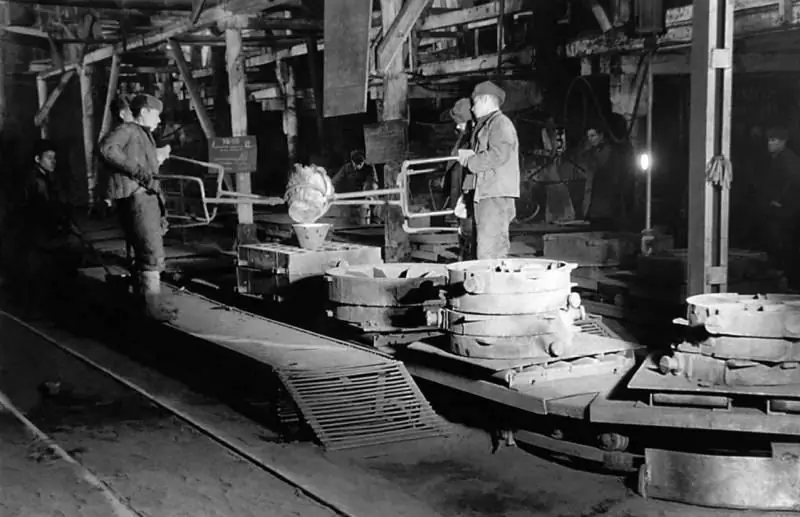
Do sredine 1942. u tvornici tenkova br. 183 situacija se razvijala na sličan način - proizvodnja čelika zaostajala je za mehaničkom montažom. A trupe T-34 morali smo „uvesti“s Uralmaša.
Jedan od razloga bio je nedostatak vatrostalnih materijala za popravak otvorenih peći, koje su u proljeće 1942. radile do krajnjih granica. Zbog toga su u jesen radile samo 2 od 6 otvorenih peći. Količine taljenja obnovljene su tek u drugoj polovici 1943. godine.
Situacija s vatrostalnim materijalima u strukturi sovjetskog obrambenog kompleksa tijekom Velikog Domovinskog rata jasno ilustrira složenost situacije u pozadini zemlje.
Kronična nestašica, općenito, ne najviše visokotehnološkog proizvoda izravno je utjecala na tempo proizvodnje oklopnih vozila.