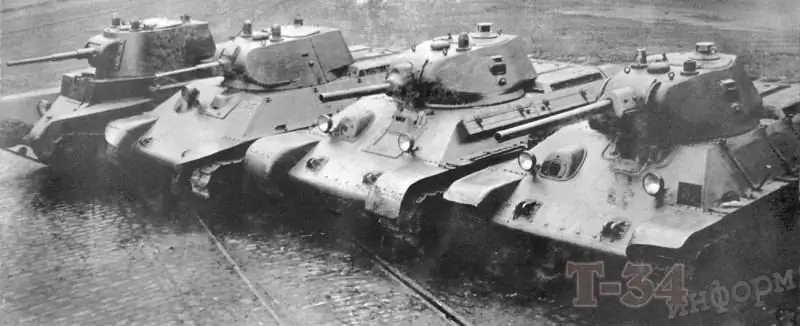
Čekajući rat
Problemi s proizvodnjom tenkova u Sovjetskom Savezu 1920 -ih i 1930 -ih, povezani prvenstveno s nedostupnošću industrije, djelomično su se objašnjavali zaostajanjem oklopne industrije. Do početka 1932. samo su dva od planirana četiri poduzeća mogla topiti i valjati oklop. To su bile tvornice Izhora i Mariupol. Zbog pretjerano visokih zahtjeva za brzinom proizvodnje (to je bio znak tog vremena), ove su tvornice kronično zaostajale za planovima. Dakle, u jednom od najstarijih poduzeća u zemlji, tvornici Izhora u gradu Kolpinu, za godinu dana uspjeli su savladati samo 38% plana, a u Mariupolju u tvornici Ilyich - samo jednu četvrtinu. Tome je uvelike pridonijela proizvodnja složenih cementiranih heterogenih oklopa, koje su kod nas znali izrađivati od 1910. godine. Slična vrsta oklopa bila je potrebna za izdržavanje projektila i metaka oštrih glava, što uobičajena homogena srednja i niska tvrdoća nisu osigurali. U to vrijeme cementirani oklop bio je podijeljen u dva razreda: nisko temperirani, jednostrano cementirani s dovoljnom tvrdom stražnjom stranom i, u drugoj verziji, sa srednje tvrdom stražnjom stranom. U osnovi, za proizvodnju takvih "sendviča" potreban je krom-molibden i krom-nikal-molibden čelik, što je zahtijevalo oskudne uvezene aditive od ferolegure. Glavni legirajući element ovih čelika bio je krom (1, 5-2, 5%), koji potiče intenzivnu karburizaciju i postizanje visoke tvrdoće cementiranog sloja nakon kaljenja. Pokušaj korištenja domaćeg mangana i silicija za čelik kaljen kućištem umjesto uvoznog kroma dao je negativan rezultat. Kada je legirano s manganom, otkriveno je da je čelik sklon rastu zrna na temperaturi rasplinjavanja (920-950 stupnjeva Celzijusa), posebno pri dugim izlaganjima potrebnim za karburiranje na velikoj dubini. Korekcija pregrijanog sloja karburizacije tijekom cementacije predstavljala je značajne poteškoće i bila je povezana s potrebom primjene višestruke rekristalizacije, što je uzrokovalo značajnu dekarbunizaciju cementiranog sloja i olova, a također je bilo ekonomski neisplativo. Ipak, do ranih 30 -ih, cementirani oklop se koristio i u zrakoplovstvu i u izgradnji tenkova. U zrakoplovima su oklopne ploče debljine do 13 mm cementirane, poput oklopa tenkova do 30 mm. Bilo je i razvoja 20-mm cementiranog oklopa otpornog na metke, koji nije išao dalje od eksperimentalnog razvoja. Takav oklop definitivno je morao biti masivan, što je zahtijevalo golema sredstva za razvoj proizvodnje.
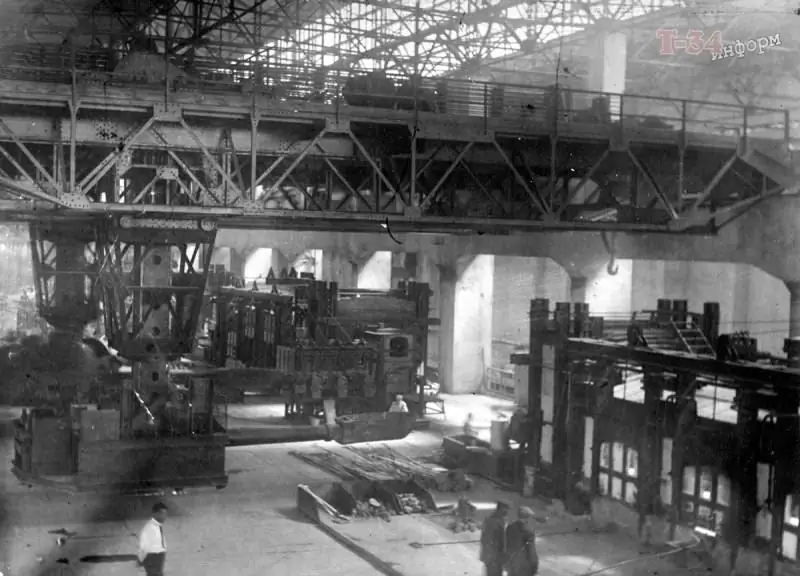
Unatoč takvim poteškoćama s proizvodnjom cementiranog oklopa, trup tenka T-28 bio je gotovo u potpunosti izrađen od njega. No, postupno je domaća industrija napuštala tehnologije cementiranja oklopnih ploča, uglavnom zbog iznimno velikog broja odbijenica. S obzirom na planove proizvodnje koje su zahtijevali vlada i specijalizirani narodni komesarijati, to uopće nije iznenadilo. Tvornica Izhora prva je prešla na novi oklop, svladavši taljenje visokotvrdog krom-silikatno-manganskog oklopa "PI". U Mariupolju su svladali heterogeni mangan "MI". Zemlja se postupno prebacila na vlastito iskustvo u projektiranju oklopa. Do tada se temeljio na stranim tehnologijama (uglavnom britanskim). Odbijanje cementiranja oklopa učinilo je ploče debljima s istim otporom oklopa. Dakle, umjesto 10- i 13-mm cementiranog oklopa, trup T-26 morao je biti zavaren od 15-milimetarskih limova izžorskog čelika "PI". U ovom slučaju tenk je bio težak 800 kilograma. Valja napomenuti da se prijelaz od skupocementiranog čelika do relativno jeftinih homogenih oklopnih tehnologija pokazao vrlo korisnim u ratno vrijeme. Da se to nije dogodilo u predratnim godinama, razvoj topljenja i valjanja skupih vrsta oklopa bio bi malo vjerojatan s obzirom na evakuaciju poduzeća u razdoblju od 1941. do 1942. godine.
Od prijeratnih godina glavnu ulogu u potrazi i istraživanju novih vrsta oklopa imao je "Institut za oklope" TsNII-48, koji je danas poznat kao NRC "Kurčatov institut"-TsNII KM "Prometej". Tim inženjera i znanstvenika TsNII-48 odredio je glavne pravce domaće oklopne industrije. U posljednjem desetljeću prije rata, pojava u inozemstvu oklopne artiljerije kalibra od 20 do 50 mm postala je ozbiljan izazov. To je natjeralo programere da traže nove recepte za kuhanje oklopa spremnika.
Rođenje 8C
Zamijenite cementirani oklop otporan na projektile i metke s oštrom glavom na lakim i srednjim oklopnim vozilima samo čelikom visoke tvrdoće. I to su uspješno savladali domaći metalurzi. Trupovi oklopnih vozila BA-10, laki tenkovi T-60 (debljina oklopa 15 mm, čeoni-35 mm), T-26 (debljina oklopa 15 mm) i, naravno, srednji tenkovi T-34 (debljina oklopa 45 mm). Nijemci su također imali prioritet oklopa visoke tvrdoće. Zapravo, sav oklop (počevši od pješačkih kaciga i završavajući zrakoplovnim zaštitnim strukturama) na kraju je postao velike tvrdoće, zamijenivši cementirani. Možda su samo teški KV-i mogli priuštiti oklop srednje tvrdoće, ali to se moralo platiti većom debljinom limova i konačnom masom tenka.
Oklopni čelik 8C, osnova protutopijske obrane tenka T-34, postao je prava kruna kreativnosti domaćih metalurga. Valja napomenuti da su proizvodnja oklopa 8C u predratnim godinama i tijekom Velikog Domovinskog rata bila dva ozbiljno različita procesa. Čak i za predratnu industriju Sovjetskog Saveza, proizvodnja 8C bila je složen i skup proces. Uspjeli su to uspješno savladati samo u Mariupolju. Kemijski sastav 8C: C - 0,22-0,28%, Mn - 1,0-1,5%, Si - 1,1-1,6%, Cr - 0,7-1,0%, Ni - 1,0-1,5%, Mo - 0,15-0,25%, P - manje od 0,035% i S - manje od 0,03%. Za taljenje bile su potrebne otvorene peći kapaciteta do 180 tona, koje su izlijevale budući oklop u relativno male kalupe od po 7, 4 tone. Deoksidacija tekuće legure (uklanjanje viška kisika) u peći provedena je skupom difuznom metodom pomoću ugljika ili silicija. Gotovi ingot izvađen je iz kalupa i valjan, nakon čega je uslijedilo sporo hlađenje. U budućnosti se budući oklop ponovno zagrijavao na 650-680 stupnjeva i hladio na zraku: bio je to veliki odmor, osmišljen da čeliku da plastičnost i smanji krhkost. Tek nakon toga bilo je moguće čelične limove podvrgnuti mehaničkoj obradi, budući da ih je kasnije kaljenje i nisko temperiranje na 250 stupnjeva učinilo pretvrdim. Zapravo, nakon završnog postupka stvrdnjavanja s 8C, bilo je teško učiniti bilo što drugo osim zavariti tijelo iz njega. No i ovdje je bilo temeljnih poteškoća. Značajna unutarnja naprezanja zavarivanja koja proizlaze iz niske duktilnosti oklopnog metala 8C, osobito zbog niske kvalitete, dovode do stvaranja pukotina koje su se s vremenom često povećavale. Pukotine oko šavova mogle bi nastati čak 100 dana nakon proizvodnje spremnika. To je postala prava pošast tenkovske zgrade Sovjetskog Saveza tijekom rata. A u prijeratnom razdoblju najučinkovitiji način sprječavanja stvaranja pukotina tijekom zavarivanja 8C oklopa bio je korištenje prethodnog lokalnog zagrijavanja zone zavarivanja na temperaturu od 250-280 stupnjeva. U tu je svrhu TsNII-48 razvio posebne induktore.
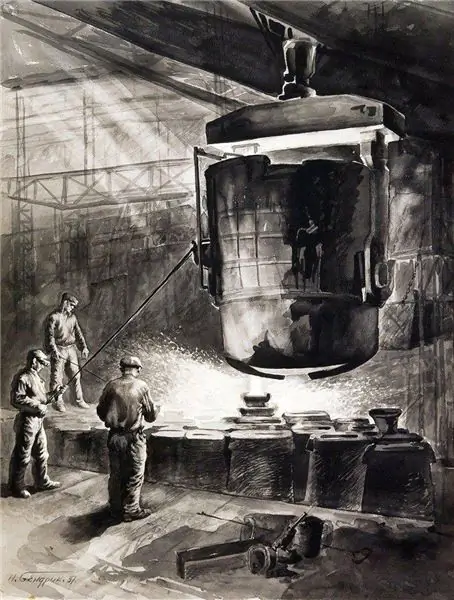
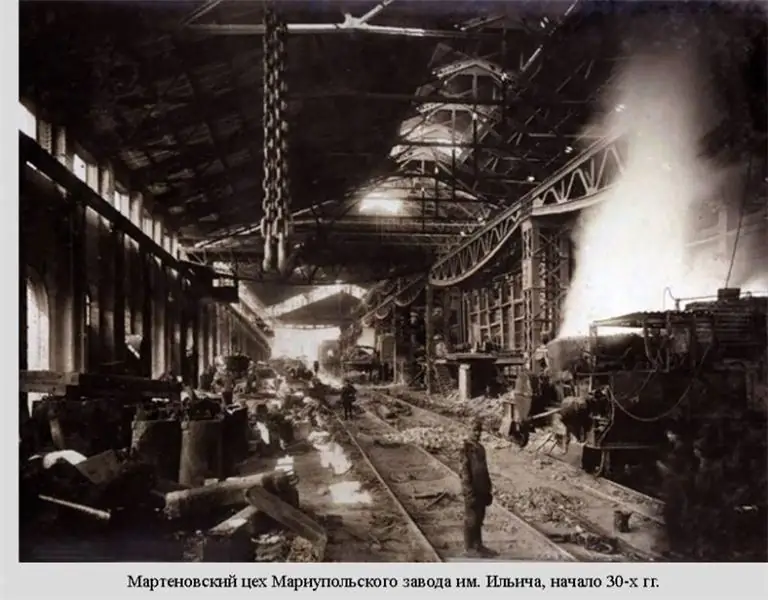
8C nije bio jedini čelik za oklope T-34. Tamo gdje je bila prilika, mijenjala se za druge, jeftinije sorte. U prijeratnom razdoblju TsNII-48 razvio je 2P strukturni oklop čija je proizvodnja značajno uštedjela energiju i pojednostavila valjanje lima. Kemijski sastav 2P: C - 0,23-0,29%, Mn - 1,2-1,6%, Si - 1,2-1,6%, Cr - manje od 0,3%, Ni - manje od 0,5%, Mo - 0,15-0,25%, P - manje od 0,035% i S - manje od 0,03%. Kao što vidite, najveća ušteda bila je u oskudnom niklu i kromu. Istodobno, vrlo niske tolerancije na prisutnost fosfora i sumpora ostale su nepromijenjene za 2P, što je, naravno, bilo teško postići, osobito u ratno vrijeme. Unatoč svim pojednostavljenjima, konstrukcijski oklop od čelika 2P i dalje je podvrgnut toplinskoj obradi - kaljenju i visokom temperiranju, što je značajno opteretilo toplinsku opremu potrebnu za toplinsku obradu kritičnijih oklopnih dijelova tenkova, a također je značajno povećalo proizvodni ciklus. Tijekom rata stručnjaci TsNII-48 uspjeli su razviti tehnologije za dobivanje sličnih čelika, čija je proizvodnja oslobodila resurse za glavni oklop 8C.